In stories from legend and antiquity, swords have a special place. From Hrunting, the sword of Beowulf, to Excalibur, sword of King Arthur, they are the centerpieces of countless myths. Because of the high regard in which swords are held, bladesmithing – the process of creating a sword – has long been regarded with fascination and awe, as if it was an almost magical process. Historical sources describe those makers of legendary swords with reverence, glorifying their skill and attributing to them sometimes mystical abilities.
This has led in modern times to an overall fascination with bladesmithing that is, unfortunately, divorced from any practical knowledge of the craft – resulting in confusion about what the process actually entails. Pop culture has contributed to this confusion as television and films often depict the process of sword making with wild inaccuracies. Consider the opening scenes of Conan the Barbarian (1982) in which a steel sword is poured into a mould, a process reserved for softer metals such as bronze. How many sword collectors based their understanding of bladesmithing on that scene? Beyond the folklore and mysticism, beyond the films and television shows, the process of sword making, while indeed complex, is not arcane in nature.
Collectors and fans of swords both historical and legendary have long been fascinated with the process of making a sword. To respond to this curiosity, we wanted to answer some of the more common questions we receive from our fans and customers: How are swords forged? And more specifically, how does Darksword Armory manufacture their swords? We will also discuss what steel is used for the making of the blades and why the type of steel is an important consideration in the proper manufacturing of a sword.
The Making of a Sword
Modern European sword makers use one of three methods to create their swords. While each method can overlap, the bulk of the process is made by either one of the three methods based on the smiths’ preference and skill. Blades can either be:
- Hand forged – this method takes lumps or blocks of raw steel and uses a forge to heat it up and stretch it out into a blade shape. Hammers and anvils, and sometimes power hammers, are used for most of the process of actually shaping the weapon, though modern tools such as belt sanders may be used for polishing.
- Stock removal – starting with a “blank,” or a long strip of pre-shaped steel, this method uses modern tools to remove enough steel from the blank to reveal the blade within. Belt grinders, sanders, and other power tools are used in lieu of traditional hand forging methods.
- CNC machine made – a CNC (Computer Numerical Control) machine is a device that uses computer technology to control machine tools such as grinders, routers, mills, and lathes. A design is entered into a CNC machine’s computer, which directs the use of tools in a process similar to stock removal on a piece of steel. As CNC machines are highly specialized, this is the most expensive method of sword making, due to the cost of the CNC machinery itself, and relies on the least amount of traditional tools and labour.
Darksword Armory uses a combination of hand forging and stock removal to create our blades, relying on both traditional forging techniques and modern machine tools. The following is a step-by-step account of our process, transforming a piece of steel into the Darksword in your hands.
Steps to Creating a Darksword
We begin with a 2” by 30”, (7mm thick) blank of 5160 high carbon spring steel. 5160 is a steel/chromium alloy with excellent toughness and resilience, making it perfect for sword blades.
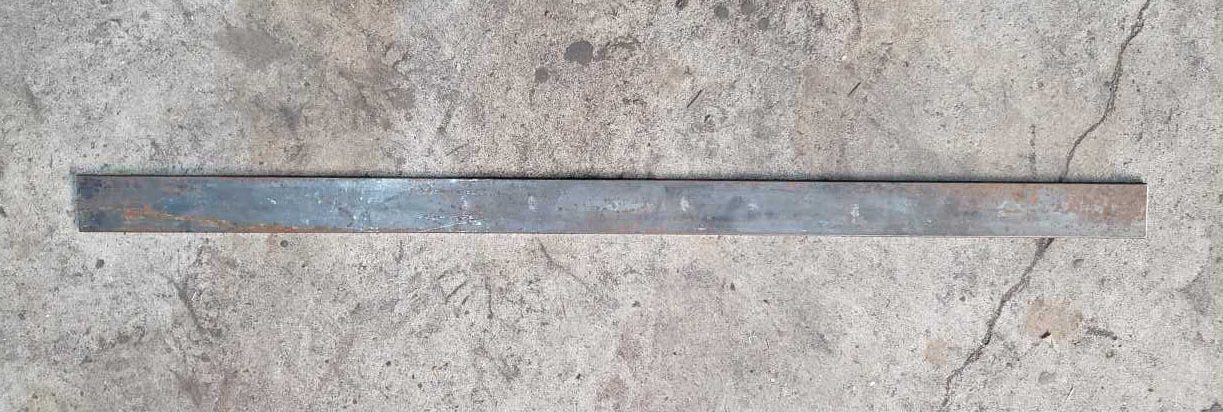
We prepare the blanks by cutting the end on one side at a 30-degree angle. This allows us to reduce the manufacturing time on making of the tip of the blade, which can be time consuming, while favouring a more symmetrical finish once we start shaping the tip of the blade. This process usually requires the tip to be heated twice prior to completion.
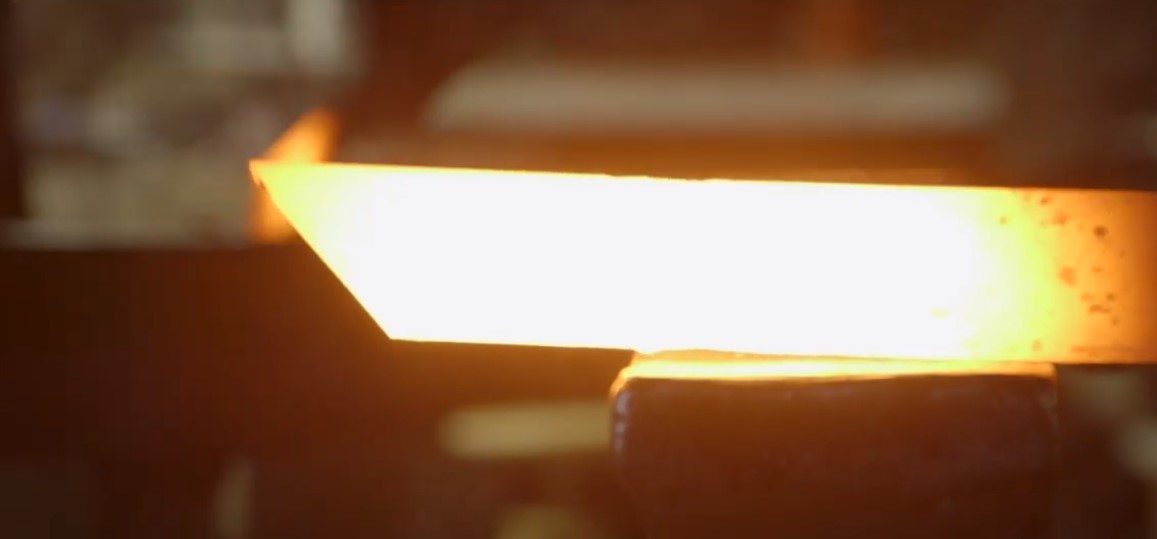
Once the tip has been shaped, we begin to “draw” the blade (hammering it into the general shape of the sword blade it will become) in the traditional manner (with hammer and anvil). We usually have 6 bladesmiths working in the shop at this point, each one working on one blade at a time – taking intervals between heating and hammering. Once the general shape is outlined, we complete the majority of the shaping on our power hammer.
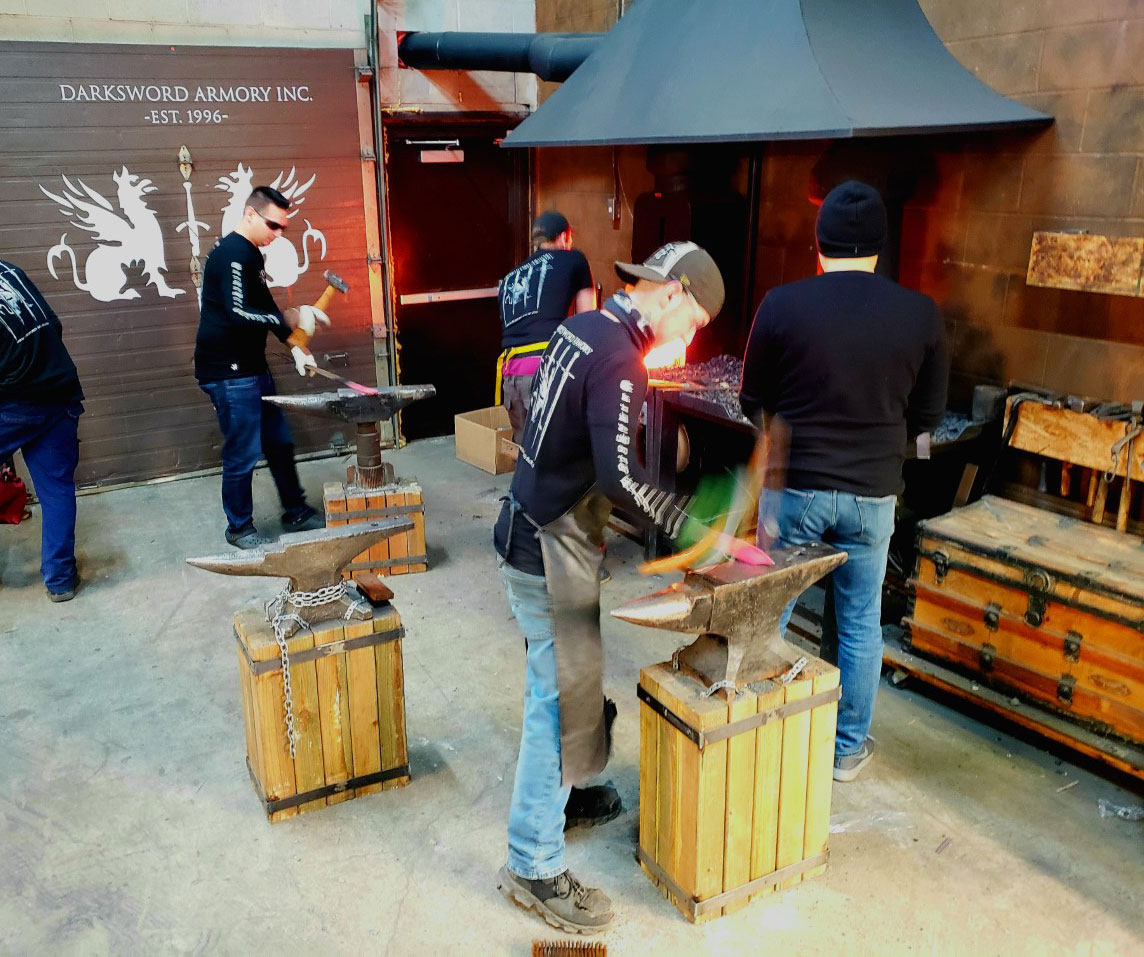
Fine adjustments to the shape of the blade are carefully made with a hammer and anvil. Each blade is examined during the forging process, in terms of its geometry and tapper – which is later further adjusted with industrial grinders prior to the tempering of the blade.
Once the blank has been transformed we work on the opposite end, drawing the tang. The tang is primarily done with the power hammer and finishing touches are made manually on the anvil. While each sword has its own attributes, the tang thickness and width remains the same among sword types. Only the length changes – which is why we work with a master prototype of each blade typology we make.
After the blade and tang have been drawn, minor adjustments are made to the geometry of the blade by use of various belt sanders and grinders. The profile is corrected, the edges are tapered, the blade tapering is adjusted, and imperfections and waves are smoothed over the grinder using various grit sanding belts. This is similar to how stock removal processes are done, though without the initial shaping in the forge that is a part of our process.
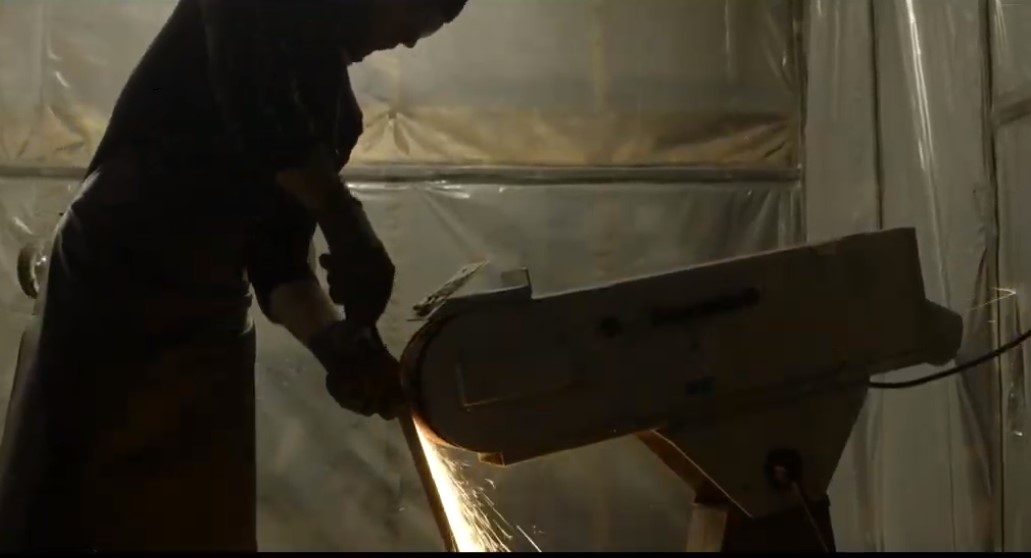
Once the blade has arrived at a shape close to the intended design, we proceed in grinding the fuller using a special 2” grinding wheel. With steady hands, we make sure that the fuller is straight, and symmetrical on both sides. Once complete, the blade goes back to grinding on the main industrial grinder to smooth out any imperfections and guide the blade to its final form.
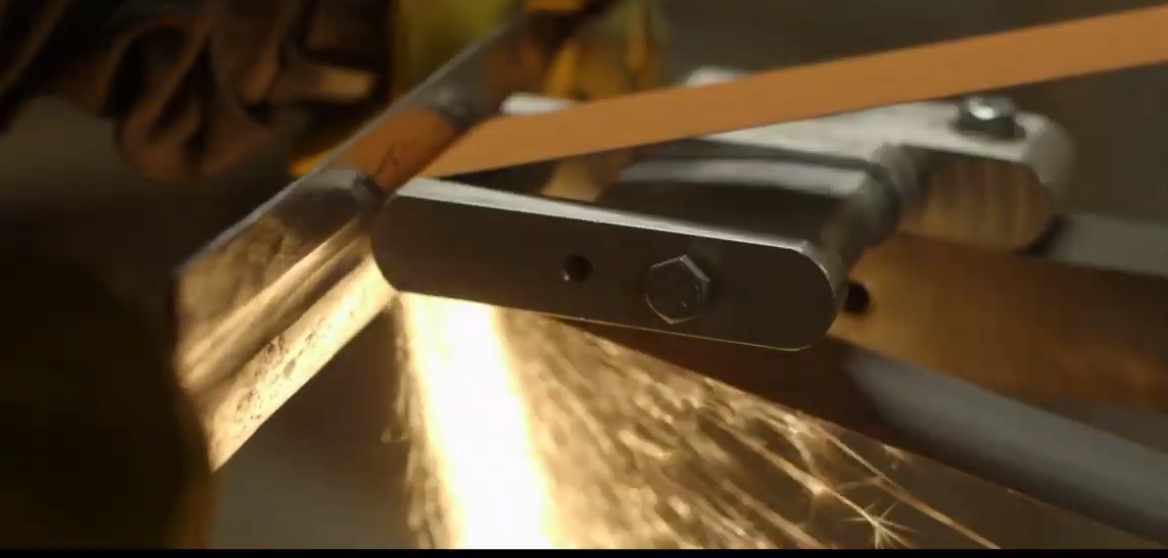
Now, the shaping work has been completed, and it is time to heat treat the blade. Blades are placed together in a large heat treating oven – or kiln – then are individually quenched in canola oil in a quenching tank.
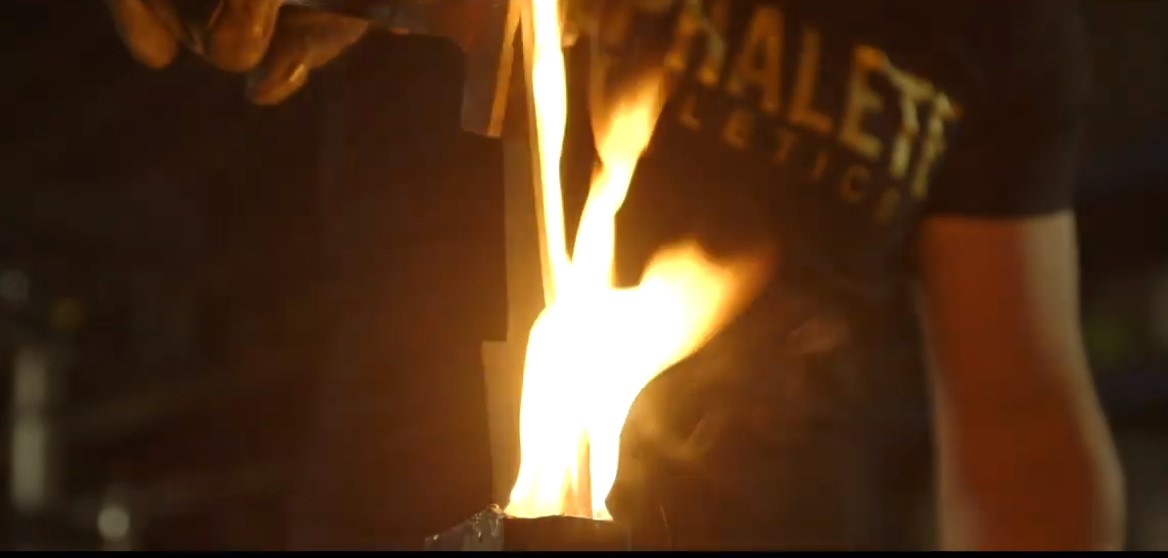
Once the blade has been quenched, we arrive at the final stages in the manufacturing process.
Post-quench, the finish on the blade is pretty rough looking. The blade must then be polished and brought to its final state before assembly. This is a lengthy process, involving various polishing wheels, compounds, different grit sandpaper pads, and finally polishing again with scotch wheel pads. All of this goes towards giving each Darksword a finish worthy of a museum piece.
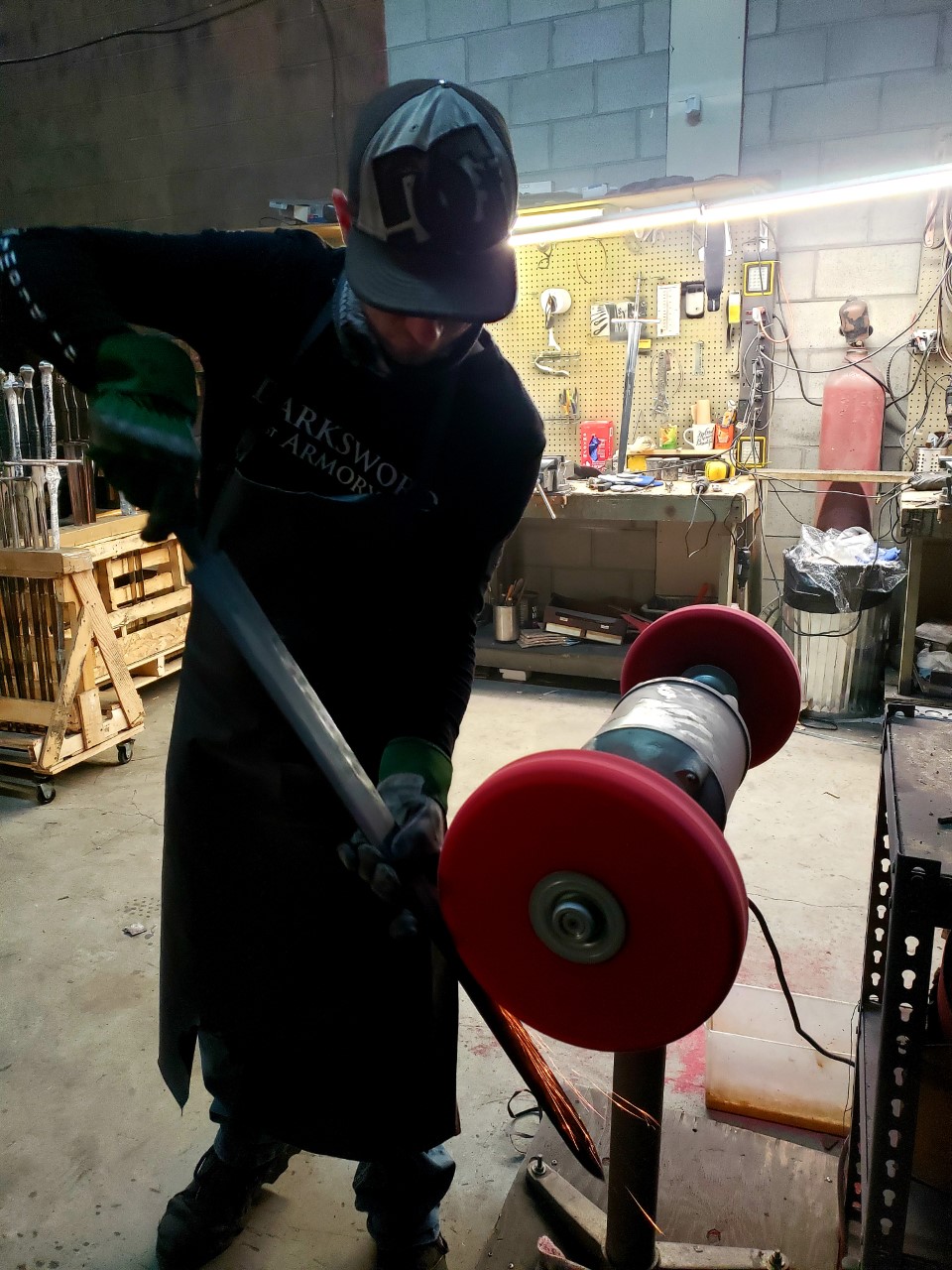
At this stage the blade is complete and moves to the assembly department. This is where blades are paired with sword fittings, which we also make in house – the guards and pommels are cast in using the “lost wax” process, moulded from an original piece designed and made at the Darksword shop.
In assembly we have 2 specialized staff members fitting the handles, guards, and pommels to the completed blade. This may involve some reshaping of the interior of the handle to ensure it has a tight fit to the tang. To reduce any possibility of movement of the fittings due to humidity or temperature change, Darksword Armory (as do most companies) also uses epoxy to secure the grips to the tang of the blade.
When the guards, handles, and pommels are in their final position the tang is peened. This means the exposed portion of the tang is heated and then hammered over the pommel, completing construction – a new Darksword is born!
To view all these steps, you can click the link below:
We hope that this peek behind the curtain at Darksword Armoury has been illuminating for you. The process we used was arrived at using countless hours of research and practice, and we are always working to improve our products. By bringing together traditional forging techniques with updated tools and methods, we aim to keep the knowledge of sword making close at hand while also benefitting from all that modern technology can bring. Now, when you purchase you next Darksword, you will have a better understanding of the process that brought it to life.